Concurrent Design: Coal Bulk Terminal Design Based On Integrated
Simulation Methods
From Proceeding of Summer Computer Simulation Conference,SCSC95, Ottawa, July 24-26 1994
Roberto Mosca, Pietro Giribone, Agostino G.Bruzzone
THE SIMULATION MODEL
It was decided to structure the plant in question by referring to the simulation based on the concept of Object-Oriented
Design (OOD).
This approach was used to make improvements to the model in successive phases, thus re-directing it towards what is
required by plant designers as the design detail evolves.
The model was implemented on personal computers to guarantee compatibility with the tools used by the company that
managed the project and was developed in C++ to optimize the performances in terms of time and portability, as well as
the useful life of the model.
The key objects modeled refer to the following plant operating components:
Belts
Belt connection towers
Stacker/Reclaimers
Ship loaders
Ship unloaders (Bucket)
Ocean-going vessels
Lighters Yards
Users
Since it is a stochastic simulator, it defines all the "uncertain" variables (fault time, component wear, maintenance
duration, berthing delays, bucket operation times, etc.) through the relative probability distributions.
During the simulation, the values are extracted from the corresponding distribution using the Montecarlo method.
The plant in question involves typically discrete operations (reclaimer handling, ship incoming operations,
fault/maintenance management, etc.) with others that are continuous by nature (flows on belts, quantity accumulated in the
yards, etc.). For this reason it was decided to develop a hybrid simulator (continuous/discrete) that correctly reproduces
system operations.
With this approach the differential equations which connect the continuous variables (e.g. continuity equations on belts)
are integrated with numerical calculation techniques in the interval between two successive discrete events.
This drastically reduces the internal discontinuities in the integration interval, thus greatly accelerating the numerical
calculation. On the other hand, the hybrid approach is used to obtain a correct estimate of the behavior of continuous
variables which with a traditional event-oriented approach would be heavily discretized.
The modeling performed on the flows on single belts utilized the following equations:
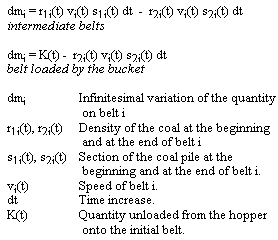
This modeling technique offers excellent precision with very low simulation times (about 5 minutes of real time for one
year of simulation on a 486 computer).
The model was equipped with an interactive graphic interface to study the operating specifications of the synoptic control
panel to be used in the real plant. Therefore, the first logical and functional validation of the model occurred graphically
by checking the flows over time in a graphic qualitative manner.
The next step involved calibration of the internal variables for which it was not possible to measure the values and, in
particular:
the variables which control the flows of ships
the variables which control the fault rate of the plant
components as a function of their operation.
In fact, basically ordinary and extraordinary type faults were studied (based on the analysis of historical times available on
similar plants operating in the area).
Extraordinary faults are modeled to occur every *ts minutes, calculated with
reference to the mean and standard deviation of normal distributions. Instead, ordinary faults occur every *to minutes of
standard operation; therefore, the interval in this case depends on the time and operating modalities of the belt.
An analog check of the simulation outputs was performed to identify the corrected values for all these parameters.
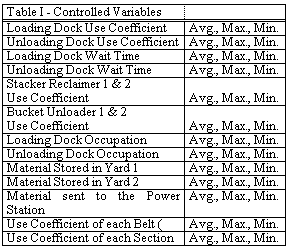
Once the check was completed, a statistical validation was carried out by studying the time development of the mean
square pure error of the simulator relative to the controlled output variables:
Coal Flows
Quay Use Coefficients
Stacker/Reclaimer Use Coefficients
Conveyors Use Coefficients
Delay on Loading/Unloading Operation
The development of this curve showed an optimum run time equal to one year of simulation, which produces significant
results in just a few minutes of real time.